In quasi tutte le applicazioni che hanno a che fare con compressori, turbine e motori si generano delle vibrazioni che ovviamente si ripercuotono anche sui sensori di misurazione. Senza le dovute precauzioni questo può pregiudicare la funzionalità dei trasmettitori di pressione utilizzati.
Le ripercussioni delle vibrazioni sui sensori di pressione possono essere gravi. Da un lato il segnale di misura può essere disturbato dalla sovrapposizione. Se la vibrazione si propaga al segnale di uscita, gli utenti otterranno misurazioni non utilizzabili. Questo effetto si nota subito senza ritardo. Inoltre, un carico continuo può portare a una fatica dei materiali. Le saldature possono rompersi e le viti allentarsi. Che provochino misure falsate o che facciano rompere i collegamenti meccanici, le vibrazioni posso rendere i sensori di pressione inutilizzabili. Per fortuna, è possibile ridurre al minimo questi effetti indesiderati.
Tecnica di misura della pressione: prevenire i danni causati dalle vibrazioni
La prevenzione è il miglior provvedimento possibile. Questo prevede che gli utenti siano a conoscenza delle vibrazioni che avvengono all’interno della loro specifica applicazione. Dunque, come primo passo è necessario determinare la frequenza di vibrazione di un’applicazione. Le vibrazioni di per sé non causano danni. Nelle schede tecniche fornite dai produttori viene spesso indicato sotto “verifiche” in quale gamma di frequenza non compaiono guasti. Per stabilirlo si applica la norma DIN EN 60068-2-6. Nella procedura di prova descritta il campione viene sottoposto ad una determinata gamma di frequenza per un tempo prestabilito. L’obiettivo è definire le frequenze caratteristiche del campione. La procedura di prova è illustrata nell’immagine.

Immagine 1: qualificazione di un prototipo:il sensore di pressione è avvitato ad un blocco di alluminio che viene sottoposto ad un carico meccanico (vibrazione, accelerazione).
Se si registrano forti vibrazioni che superano le specifiche del sensore di pressione, si prendono in considerazione innanzitutto due approcci. Il primo approccio riguarda la dimensione spaziale: quanto è grande il trasmettitore di pressione e dove va montato? Più il trasmettitore di pressione è pesante e grande, maggiore è l’effetto delle vibrazioni e minore la resistenza. Nelle applicazioni interessate da forti vibrazioni può quindi essere vantaggioso utilizzare un sensore di pressione piccolo, come ad esempio l’ATM.mini che,per via della sua massa ridotta, viene poco condizionato dalle vibrazioni.
Oltre alle dimensioni del trasmettitore di pressione conta anche la sua posizione nell’applicazione. Se, ad esempio, il sensore si trova sull’asse delle vibrazioni, subisce meno vibrazioni. Se, però, viene montato trasversalmente all’asse delle vibrazioni, deve reggere l’intero carico di vibrazioni.
In aggiunta, è possibile equipaggiare il trasmettitore di pressione stesso in modo tale che resista meglio alle vibrazioni. In questo caso il sensore viene impregnato di un composto morbido che ammortizza le vibrazioni, proteggendo così le parti meccaniche. Nell’immagine 2 si può vedere questo composto trasparente e lucido.
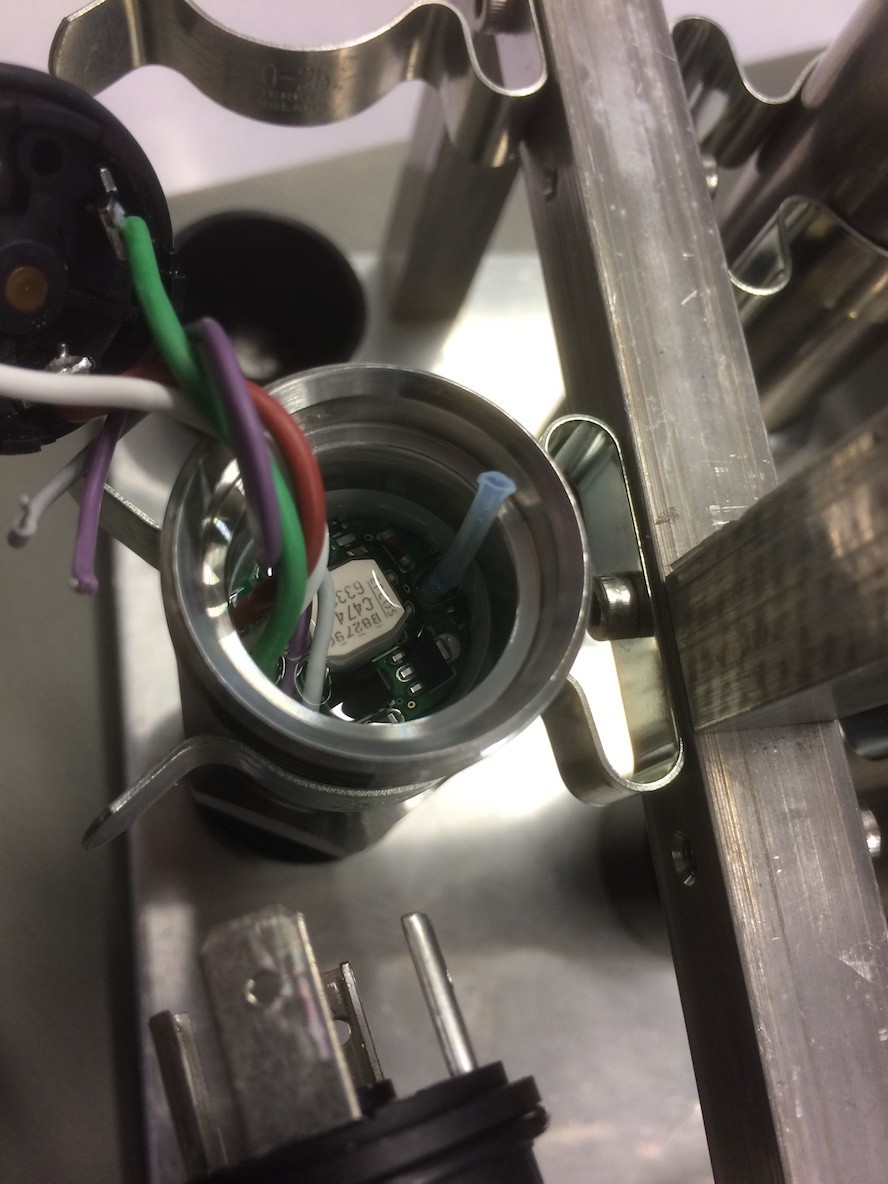
Immagine 2: Sensore di pressione con il composto
In sintesi possiamo affermare che le forti vibrazioni possono danneggiare i sensori di misura. Scegliendo un sensore di pressione adatto all’applicazione specifica (gamma di frequenza, dimensioni) e un montaggio ottimale (ad es. sull’asse delle vibrazioni) è possibile ridurre gli effetti delle vibrazioni. Un’ulteriore protezione è offerta dal composto ammortizzante con cui si può bagnare il sensore (vedi immagine 2).